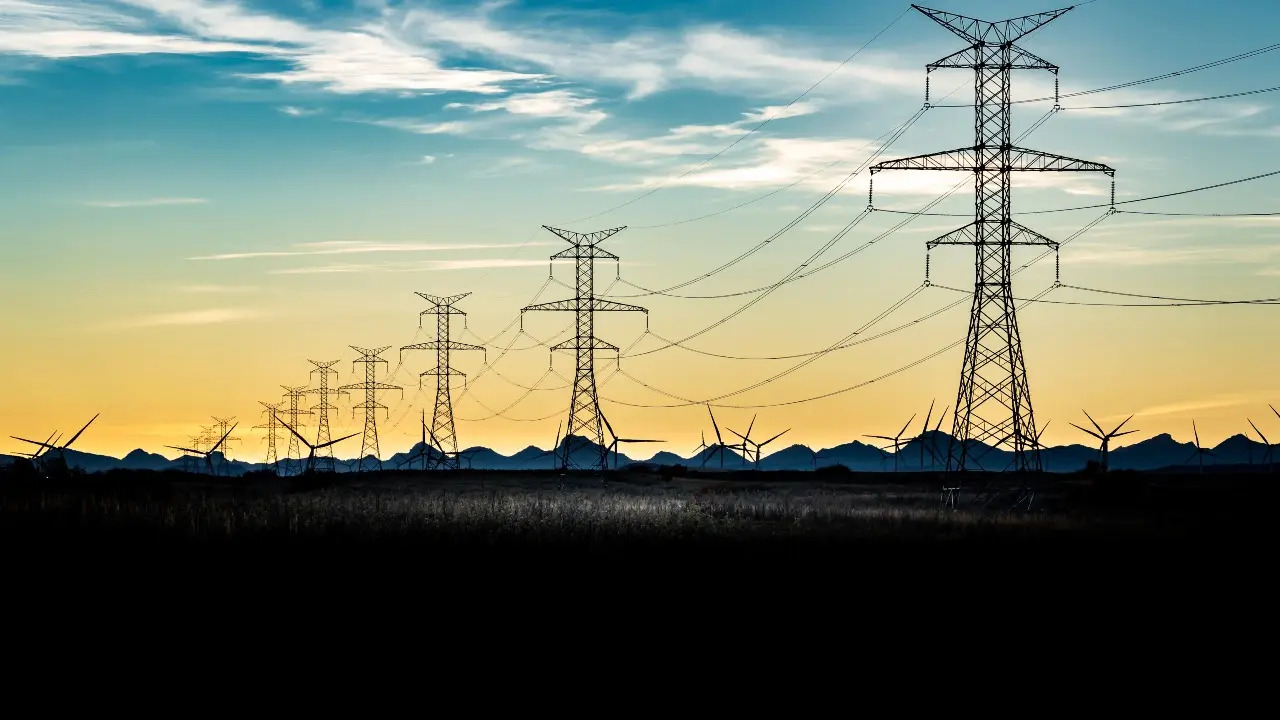
Дефекты ЛЭП будут выявлять в Казахстане с помощью искусственного интеллекта
- Posted by admin
Инновационный цифровой сервис предназначен для автоматического выявления дефектов на воздушных линиях электропередачи. Новая система использует данные с беспилотных летательных аппаратов, включая видео, фотографии, тепловизионные и LiDAR-измерения, что позволяет эффективно и точно контролировать состояние сетевой инфраструктуры.
Сервис является частью информационной платформы "Единая государственная система управления топливно-энергетическим комплексом" (EnergyTech) и способствует цифровой паспортизации объектов с привязкой обнаруженных дефектов к конкретным техническим участкам. Применение обучаемых нейросетей обеспечивает высокую точность выявления неисправностей – до 98%.
"Системы создаёт отраслевой дата-центр визуальной информации с эталонными выборками, который служит для постоянного переобучения моделей искусственного интеллекта и повышения эффективности диагностики. Также предусмотрены сценарии автоматической маршрутизации выявленных дефектов в системы технического обслуживания и ремонта", – пояснили в ведомстве.
Как отметили в Минэнерго РК, интеграция новой технологии в платформу EnergyTech закладывает основу для перехода к проактивной диагностике и цифровому техническому надзору, что способствует снижению аварийности и повышению надёжности электросетей передачи и распределения электроэнергии.
Фото: Depositphotos.com